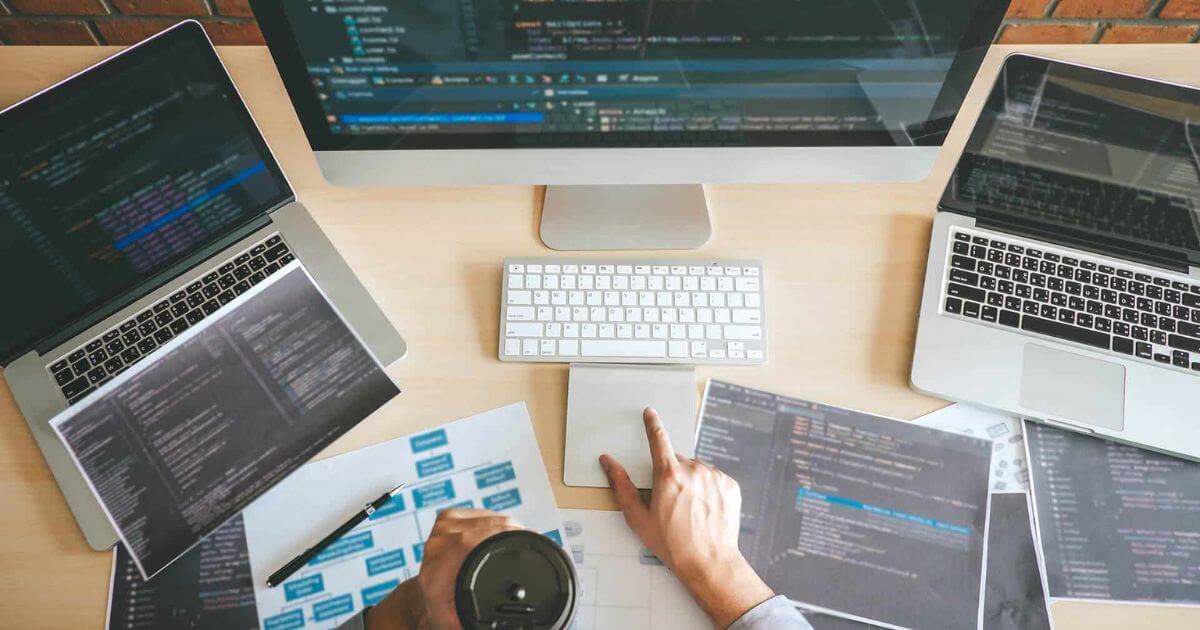
Charge Converter
Convert electric charge units quickly and accurately.
Electric charge stands among the most fundamental concepts in physical science, underlying the behavior of electrons, protons, and ions that form the basis of electricity. Interactions grounded in electric charge power nearly every corner of modern technology, from computing devices and sensors to large industrial equipment. Yet measuring, managing, and converting that charge is not always straightforward. Even the term “Charge Converter” can refer to multiple domains: it might be an electronic instrument that converts high-impedance signals from piezoelectric sensors into more manageable, lower-impedance voltages; it could be a piece of power-handling hardware that facilitates battery charging under variable conditions; or it might be a simpler software tool or mathematical routine that translates numeric charge values among various units (such as coulombs, ampere-hours, or faradays). In essence, “Charge Converter” can describe any device or process that transforms one representation or form of electric charge into another, bridging a potential gap in measurement, usage, or engineering context.
This comprehensive deep-dive will explore each angle. From clarifying electric charge as a physical property to spotlighting the hardware-based charge converters used in instrumentation, from describing potential usage in battery-charging modules to showcasing the difference between small laboratory sensors and massive industrial setups, we will map out the diverse usage scenarios. Along the way, we will illustrate the intricacies of unit conversions for charge, show how advanced electronics convert signals for measurement or control, and examine how large-scale charging infrastructure harnesses the concept of “charge conversion” to shape modern transport, instrumentation, and power electronics. The goal is to arm you with a broad, detailed understanding of what a “Charge Converter” can mean in practice, why it is so essential, and how it anchors the interplay of technology and physics in everyday life.
The Fundamentals of Electric Charge
All matter built from atoms contains charge-bearing particles: negatively charged electrons and positively charged protons. Net charge in a system arises from an imbalance between these charges—more electrons than protons leads to net negative charge, and vice versa. The coulomb (C) is the SI base unit for electric charge, defined in terms of the elementary charge (the charge of one proton or the negative of one electron). It is a direct measure of how many electrons (or electron equivalents) are effectively present as surplus or deficit. One coulomb corresponds to the charge carried by approximately (6.242 \times 10^{18}) electrons, an enormous count.
When charge moves, we talk about electric current. One ampere of current means one coulomb of charge passing a point per second. But charge itself can also be a static property (accumulated on a capacitor or on an object in an electrostatic setup), or it can appear as a dynamic, time-varying property in circuits. In any case, measuring or controlling the flow of charge is central in electronics, power distribution, communications, sensors, and more.
Common Units of Charge
While the coulomb is the standard, certain sub-multiples or alternative units exist:
- Coulomb (C): The SI base measure for charge.
- Microcoulomb (μC), Millicoulomb (mC), Nanocoulomb (nC): For smaller scales, typical in sensor readouts, electroplating, or lab contexts.
- Ampere-Hour (Ah): More typical in battery usage. Since 1 Ah = 3600 coulombs, a battery rated 2 Ah can supply 2 amperes for an hour (7,200 coulombs total).
- Faraday: In electrochemistry, 1 faraday is the charge of 1 mole of electrons (~ 96,485 C).
- Elementary Charge (e): For particle physics or extremely small signals, referencing multiples of e (~ (1.602 \times 10^{-19}) coulomb).
Where “Charge Converters” in a purely numeric sense might revolve around software or formulas to convert a given numeric quantity in coulombs to ampere-hours or vice versa, in hardware usage, “charge converter” implies something different: an electronic or electromechanical device that reinterprets or shapes charge signals.
Charge Converter as a Unit Conversion Tool
A simpler notion of “Charge Converter” is an online or software-based system that switches among different numeric units of electric charge. For example, a researcher analyzing a tiny sensor might measure 50 microcoulombs, wanting to compare that to millicoulombs or coulombs. Or an electrochemist might log how many faradays pass in a reaction. Because 1 coulomb is neither extremely large nor small for many real-world tasks, bridging units is frequent.
Typical Functionality
- Input: The user provides a numeric quantity (like 3.5) and picks the known unit (e.g., coulomb).
- Output: The user chooses a target (like microcoulomb), and the converter multiplies or divides by (10^6).
- Lists: Some converters handle up to 17 or more units, such as coulomb [C], millicoulomb [mC], microcoulomb [μC], kilocoulomb [kC], megacoulomb [MC], ampere-hour [Ah], milliampere-hour [mAh], faraday, or base electron charges.
This approach can be integrated simply with programming logic or a website’s JavaScript. The main complexity is ensuring accurate numeric factors for each unit, especially if bridging to less common measures. While essential for some educational or scientific tasks, this version of a “charge converter” is only one dimension. The next dimension is instrumentation-based.
Charge Converters for Sensors and Instrumentation
In certain sensor technologies, especially piezoelectric transducers (like accelerometers, pressure sensors, or force sensors), the device outputs an electrical charge proportional to the mechanical deformation. Because the sensor is effectively a capacitor generating or releasing small amounts of charge, the output is a high-impedance signal. Long cables or typical data acquisition systems cannot measure such high-impedance signals easily or cleanly. The solution? A “charge converter,” also called a “charge amplifier” or “charge-to-voltage converter,” which transforms that minute, high-impedance charge into a low-impedance voltage effect that standard instrumentation can read reliably.
Operating Principle
- Charge Input: The sensor produces a charge (Q) in coulombs, typically very small (microcoulombs, nanocoulombs, or even picocoulombs).
- High Impedance: Direct measurement is tough because any cable or measuring device with finite input impedance can dissipate or leak the charge.
- Charge Amplifier: A specialized operational amplifier with a large feedback capacitor is used. The input is fed to the amplifier inverting terminal, the feedback capacitor accumulates the charge, and the output voltage becomes ( V_{out} = -\frac{Q}{C_{feedback}} ).
- Low Impedance Output: The resulting signal is a standard voltage in some range, typically ±5 V or 4–20 mA, etc., depending on design. This can be cabled to normal data acquisition hardware.
- Inline or External: The “charge converter” might be a small inline device placed near the sensor or a dedicated box in a lab. Some industrial setups incorporate them into the sensor itself.
Typical Use Cases
Piezoelectric accelerometers for vibration monitoring, dynamic pressure sensors, shock sensors, or test-lab strain gages can produce only an electrical charge. For condition monitoring, analyzing rotating machinery, or measuring mechanical shock in automotive or aerospace tests, a reliable charge converter ensures those signals become stable, noise-resistant voltages traveling across cables to recorders or real-time displays.
Inline ICP® Technology
One subtype is “ICP®” or “IEPE” sensors that incorporate built-in microelectronic charge converters inside, so they output a low-impedance voltage. In older or more specialized sensors, the user might rely on an external charge converter. The “ICP® charge converter” is basically a mini amplifier. With an external supply, it shifts the sensor’s minuscule, high-impedance charge signal to a consistent, standardized voltage signal. This approach simplifies cabling, though the device still is a specialized piece of “charge converter” electronics.
Converters for Battery Charging and Power Electronics
In the domain of power electronics, “charge converter” might describe hardware that conditions or changes the charging profile. For instance, an RV converter/charger transforms AC mains into DC to charge an onboard battery bank, controlling both voltage and current to ensure safe, rapid, or float-charging modes. This usage often merges with the notion of a “charger” or “DC-DC converter that manages battery charge.” While the device is not measuring or amplifying a small sensor charge, it is converting line electricity into a carefully managed DC charge for batteries. Some key areas:
-
RV and Marine Converters
- Typically called “converter-chargers,” they rectify 120 V AC or 230 V AC into 12 V DC at controlled current levels, charging lead-acid, AGM, or lithium batteries.
- They might have multi-stage charge profiles: bulk, absorption, float, automatic or wizard-based control to prolong battery life.
- Overvoltage, reverse polarity, or overtemperature protections are standard.
-
USB or QuickCharge Modules
- A small DC-DC “buck” or “boost” converter from 12–24 V DC (like a car battery) down to 5 V USB can be considered a “charge converter,” ensuring stable 5 V for device charging.
- QuickCharge 3.0 or PD-based modules might adapt the voltage from 5 V to 9 V, 12 V, or 20 V under negotiation. Essentially, it “converts” the input supply into an appropriate DC output for charging phones, tablets, or laptops.
-
Industrial Battery Chargers
- Large forklift or golf cart chargers, or entire data center UPS systems, rely on power electronics that handle robust current. They might be called “charge converters” in a broader sense.
- The difference from a mere variable DC supply is the attention to battery chemistry and state-of-charge algorithms.
Though these devices might not always carry the exact name “Charge Converter,” they fulfill an integral job: bridging an input power source to a battery charge method. The crucial function is controlling how coulombs pass from the source to the battery, abiding by safe voltages, currents, and system requirements.
Advanced or Specialized Topics
Ion Beam or Particle Accelerators
In certain physics or materials labs, “charge converter” might refer to an add-on that modifies the charge state of an ion beam. For instance, a negative ion beam might pass through a “charge exchange cell,” stripping electrons to produce positive ions for subsequent acceleration. While somewhat niche, it demonstrates “charge conversion” can also mean physically changing the net charge of a beam, separate from the electronics angle.
Lab Charge Measurements
In electrochemistry or coulometry experiments, measuring total charge passing through a solution can be the basis for analyzing reaction stoichiometry. A “charge converter” might be as simple as an extremely precise current integrator that yields total coulombs passed over time. This would be a specialized amplifier circuit with an integrator function—another kind of hardware instrumentation usage.
Large-Scale Systems
Some high-voltage DC lines or advanced HVDC converter stations might incorporate gate-turn-off thyristors or IGBTs to finalize “charge-based conduction,” but that typically references large “power converters.” While not specifically labeled “charge converters,” the fundamental concept is controlling electron flow in the grid. The scale is enormous, though the principle remains shaping charge movement to meet system demands.
Charge Converters in Data Logging
When dealing with plant machinery or structural health monitoring, you might have dozens or hundreds of piezo-based sensors. Each sensor’s minuscule charge is turned to a digital measure for logging. If the sensor is “charge mode,” it demands either an inline converter or specialized channels on your data acquisition system. This is a typical scenario in large power plants, oil rigs, or wind turbine farms that rely on vibration analysis. The “charge converter” ensures each sensor’s data is cleanly available over standard wiring. Maintenance teams can quickly hot-swap sensors or converters if a component fails.
Common Considerations in Selecting a Charge Converter
- Input Range of Charge: Sensor outputs can range from picocoulombs to microcoulombs. The converter must handle the expected signal without saturation or excessive noise.
- Frequency Response: For dynamic signals, as with vibration (0.5 Hz to 10 kHz) or ballistic shock (up to 100 kHz or more), the converter must maintain faithful amplitude and phase response across the band.
- Noise Performance: Minimizing self-noise is critical to read extremely small signals. Good design with minimal leakage or offset current is key.
- Linearity: The output voltage should remain linear across the sensor’s full range of generated charge, avoiding distortion or clipping.
- Power Requirements: Some require external DC supply rails (like ±15 V or +24 V). Others run from a specialized constant-current line (ICP® concept).
- Environmental Tolerance: If placing an inline converter near a hot engine or in a humid environment, ensure it can handle those conditions.
- Cable and Connector Types: For sensor signals, specialized connectors might be used, like BNC or TNC, ensuring minimal triboelectric noise. The converter’s output might be a standard coax or a dedicated data link.
- Cost and Integration: High-end converters can be pricey, especially if they handle wide dynamic range or extreme temperatures. “All-in-one” sensor modules with integrated conversion can be simpler to field, but less flexible than separate external modules.
Example Calculation: A Piezoelectric Accelerometer
Suppose you have a piezoelectric accelerometer with a sensitivity of 10 pC/g (10 picocoulombs per g of acceleration). Your testing subject experiences up to 500 g in a shock event. That means the sensor yields up to 500 × 10 pC = 5,000 pC (5 nC). If your converter design uses a 5 nF feedback capacitor, then
[ V_{out} = -\frac{Q}{C_{feedback}} = -\frac{5 \times 10^{-9} \text{C}}{5 \times 10^{-9} \text{F}} = -1 \text{V} ]
Hence at 500 g, you see a 1 V amplitude. You want to ensure the converter can handle more than that in case of overshoot. Also, you check that the noise floor is well below your smallest expected signal. If you do sub-1 g measurements, the charge might be around 10 pC, and the converter output is about 2 mV. That is feasible if the converter noise is suitably low. This might guide your choice of feedback capacitor, amplifier, or built-in calibration resistor to ensure a stable baseline and minimal drift.
Real-World Implementation Examples
1. Condition Monitoring in a Factory
A steel mill’s rotating machinery requires continuous vibration analysis to prevent catastrophic breakdowns. Each motor or roller stand is fitted with a piezo-based accelerometer. Because these can produce up to microcoulombs of charge in high-vibration scenarios, an external multi-channel “charge converter” rack is installed in a control room. The sensors connect via shielded cables. The converter outputs ±5 V signals that feed into a data acquisition computer. Specialized software logs real-time waveforms, performs spectral analysis, and triggers alarms if vibration patterns deviate from normal.
2. On-Vehicle Testing
An automotive R&D lab instrumenting a car’s suspension picks sensors for stress and shock measurement. Because space is tight and heat is high near the wheels, the standard approach might be small charge-mode accelerometers. In-line charge converters (ICP®-style) near each sensor, or an integrated approach, ensures that signals from each corner of the vehicle come in as low-impedance lines unaffected by road or engine electromagnetic interference. The test rig then collects these signals to refine the suspension design based on real-time data.
3. Medical Ultrasound or CT Imaging
In advanced imaging, certain arrays or transducers might produce small charges. A “charge converter” stage on the transducer board ensures signals from each element are properly converted to voltages for further analog or digital processing. Minimizing noise is crucial to get clear images. While these modules might not be marketed plainly as “charge converters,” the principle is the same: small charge signals from transducer elements require specialized front-end electronics.
4. Large Battery Charging
In an RV or off-grid cabin, the user invests in a 12 V system with up to 400 Ah of battery capacity. The converter-charger is installed to connect to 120 V or 230 V mains (depending on region) whenever available, automatically charging the battery bank. The device is also a DC power supply for onboard loads. Because it handles the “charge,” one might loosely call it a “charge converter.” The built-in logic transitions from bulk charging at higher currents to a float stage, preventing overcharging.
Key Differences Between “Charge Converter” and “Charger”
These terms occasionally intermix, but they are not fully synonymous:
- Charge Converter (Instrumentation Sense): Focused on transducing a high-impedance or raw electric charge into a stable, low-impedance voltage for measurement. Principally used with sensors like piezoelectric devices.
- Charger (Power Electronics Sense): Delivers energy from a supply to a battery or storage device, controlling current and voltage over time. The “charging” process is about transferring coulombs from source to a battery.
Yes, both revolve around “charge,” but their roles differ significantly. The instrumentation device rarely deals with large energies or battery charging logic but focuses on amplified readouts. By contrast, a charger might handle large currents, but it is not measuring a sensor’s small signals. Some contexts, like “converter-charger” in an RV, do combine AC-DC conversion with charging algorithms for an onboard battery. That is a specialized subcategory bridging the concept of converting line power to DC for charge control.
Potential Pitfalls in Real Deployments
- Noise Interference: High-impedance charge signals are extremely sensitive to cable flex, triboelectric effects, or electromagnetic interference. If you place a converter or amplifier too far from the sensor, you might see spurious output. Good design often suggests short cables from sensor to converter, or integrated solutions.
- Overrange or Saturation: If your sensor experiences stronger signals than expected, you could saturate the converter. The output “clips” and data is lost. Always factor in headroom.
- Temperature Effects: Some electronics drift with temperature changes, especially if the converter is exposed to wide swings. The baseline offset or scale factor might shift. Quality designs mitigate that.
- Calibration Maintenance: Over time, feedback capacitors or internal references might degrade. Routine calibration ensures accurate sensitivity, especially in mission-critical measurements.
- Mismatched Gains: For sensor usage, the user must specify the correct relationship: if the feedback capacitor is too large, the output might be too small to measure well; if it is too small, you might saturate easily.
- Incorrect Unit: If you think you are reading coulombs but the device is actually giving a scaled output in microcoulombs, you might interpret data incorrectly by a factor of a million. Clear labeling is essential.
- Grounding: For small signals or high power, ground loops or poor grounding create huge headaches. The converter might pick up hum or produce offset. Balanced or differential approaches can help.
Future Outlook
As sensor technology evolves, the demand for high-precision, wide-band, and user-friendly charge converters continues. Meanwhile, battery technology and charging solutions are surging forward, with electric vehicles, large-scale energy storage, and advanced consumer electronics. The concept of controlling or managing electric charge remains core to these innovations. We can expect:
- Miniaturization: Microelectronic or integrated “charge converter on a chip” solutions, embedded directly in sensors, providing digital output.
- High Temperature: Harsh environment electronics for aerospace or deep drilling might require robust electronics that handle charge signals at 200 °C or more.
- Smart Charger Integration: In the automotive EV realm, advanced power converters that measure real-time battery parameters to modulate charge. Possibly combining battery health data, temperature sensors, and predictive analytics.
- AI-assisted Gains: In instrumentation, one might see algorithms that automatically optimize feedback capacitor or gain for each measurement scenario, ensuring dynamic range is fully used.
- Quantum or Nanoscale: Research sensors might produce unbelievably small charges at the quantum level, demanding ultra-low noise converters with cryogenic or extreme vacuum operation.
Though the contexts differ widely— from big automotive plants to labs studying fundamental physics— the principle of “charge conversion” or at least “charge management” anchors them all.
Conclusion
“Charge Converter” as a term can reference an array of concepts: from a simple numeric converter bridging units like coulombs to ampere-hours, to a sophisticated hardware device that transforms a piezoelectric sensor’s tiny, high-impedance output into a standard voltage, or to a robust power device that orchestrates the charging of batteries. Despite these variations,