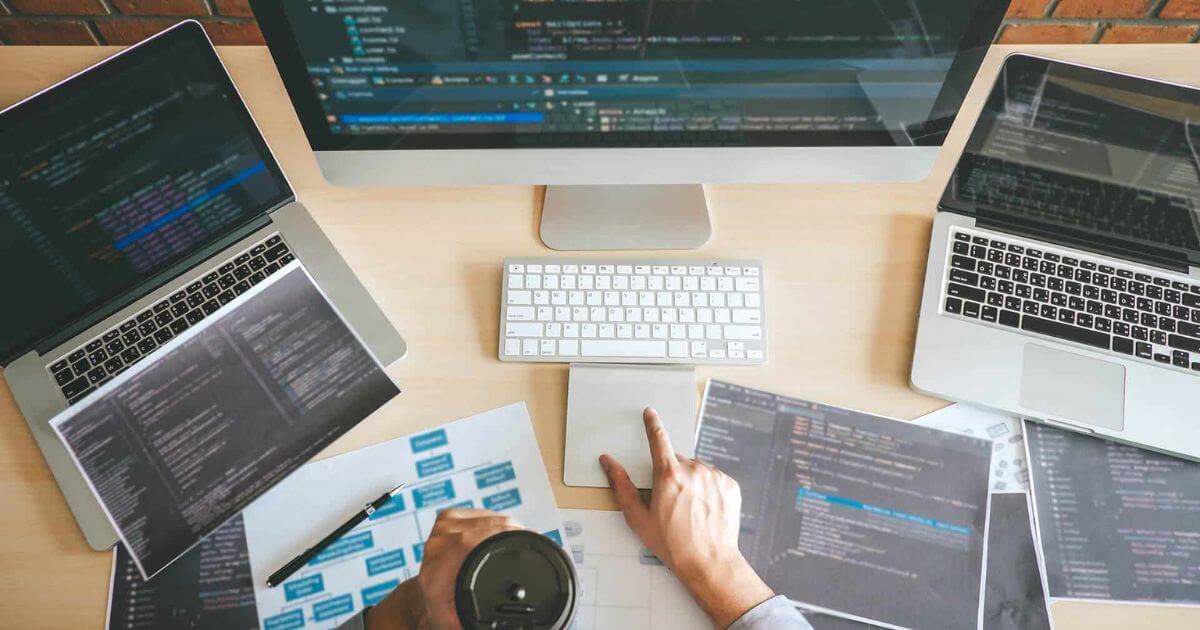
Frequency Converter
Convert frequency units quickly and accurately.
A stable, efficient power supply underpins virtually every modern system, from simple household appliances and office equipment to large-scale industrial machinery in manufacturing plants. However, not all global regions or applications rely on the same voltage or frequency. A machine built for North America might expect a 60 Hz power supply, while much of Europe and large parts of Asia operate at 50 Hz. More specialized applications, such as aviation electronics or naval systems, may demand 400 Hz. Scientific equipment and certain manufacturing processes may need advanced control of frequency for testing or specialized operation. Navigating these differing standards and the specific needs of varied systems would be nearly impossible without the Frequency Converter, a powerful technological solution designed to change the frequency (and sometimes the voltage) of alternating current (AC) power to match the requirements of a given device or environment.
While frequency conversion technology might appear specialized, it dramatically influences countless sectors—from seamlessly integrating imported equipment, to enabling traveling professionals to power their electronics abroad, to ensuring rotating machinery and motors function as expected. Through the lens of industrial automation, research laboratories, military applications, aerospace testing, and even building HVAC systems, frequency converters make it all possible. These devices, also called frequency changers, mitigate the risks of running equipment at improper frequency—such as overheating, mechanical stress on motors, or suboptimal production cycles—and offer deeper benefits like variable speed control and improved power quality.
Yet the deeper details behind frequency converters—how they function, the difference between rotary and solid-state designs, the subtleties of single-phase versus three-phase power, or the ability to switch from 50 Hz to 60 Hz or 400 Hz—can be perplexing. Add in the complexities of voltage changes, energy efficiency concerns, and specialized usage contexts (like maritime or aerospace), and it becomes clear that frequency converters lie at the crossroads of electrical engineering and real-world practicality. This article provides a detailed, sprawling examination of frequency converters, enlightening everything from how electricity around the globe differs to the engineering fundamentals behind converting AC waveforms. We delve into the underlying operating principles, typical features, industry applications, sizing guidelines, advanced control methods, cost-benefit analyses, and the future trajectory of these indispensable devices. By the end, you will gain a strong grasp of what frequency converters are, why they matter in so many contexts, and how to approach them from a user or integrator standpoint.
Understanding the Core of Frequency and Power Systems
Before plunging into the specifics of frequency converters, it is beneficial to ground ourselves in the fundamental concepts of electricity generation and distribution. Alternating current stands as the global standard for power grids, allowing efficient long-distance transmission. The rate at which the AC waveform completes one cycle per second is the frequency, measured in Hertz (Hz). In many regions, the frequency is standardized at 50 Hz, while in others—most notably North America, some parts of Southeast Asia, and a few other locales—it is 60 Hz. Meanwhile, specialized or legacy systems like certain aircraft or military-grade applications operate at 400 Hz due to the advantages of smaller equipment size for high-frequency usage.
Why Frequency Matters
Frequency is not just an arbitrary number. For many rotating devices, such as motors, the mechanical speed is directly proportional to the electrical input frequency. Therefore, a motor designed for 60 Hz supply will spin faster under 60 Hz than it would under 50 Hz. If you run such a motor constantly on 50 Hz without any adjustments, it can lead to suboptimal performance, overheating, or mechanical stress. Similar logic extends to other equipment like compressors, pumps, fans, or industrial automation lines, which rely on precise speed control for consistent output.
Beyond motors, certain electronics—especially older or simpler designs—may count on the AC frequency for internal timing circuits or ensure that a stepping motor or synchronous device receives the correct pulses. In advanced scenarios involving large-scale testing, specialized frequency settings are vital for verifying how a product behaves or stress-tests under various global power conditions. Even smaller electronics, though nowadays more universal with internal power supplies, can still run into inefficiencies or noise issues if the power frequency differs significantly from design expectations.
Global Differences in Frequency
Though 50 Hz and 60 Hz are the primary standards, the presence of niche frequencies or localized variations underscores the complexity:
- 50 Hz: Europe, Asia, Africa, large areas of South America, Australia—covering a vast majority of the population globally.
- 60 Hz: North America (USA, Canada), many parts of Central and northern areas of South America, some Asian regions.
- 400 Hz: Common for aerospace, defense, specialized generators for aircraft and naval systems.
- Variable Frequencies: Some industrial processes or test stands require adjustable AC waveforms at frequencies ranging from a few Hz up to hundreds or thousands of Hz, depending on the scenario.
Where different grids or specialized areas intersect, or where equipment from one region is used in another, frequency mismatch rears its head. Voltage is another mismatch but can often be transformed with simpler transformers, while adjusting frequency is less straightforward. Enter the frequency converter.
Frequency Converters Unveiled
A frequency converter is an electrical or electromechanical device that takes in AC power at one frequency and outputs AC power at another frequency, typically with the same or user-specified voltage. Converters can be large or small, from portable desktop units used to operate lab equipment from foreign markets, to large industrial motor-generator sets that handle tens or hundreds of kilowatts for entire factories or ship-based systems. They can be broadly categorized into two main technologies:
-
Rotary (Motor-Generator) Converters:
Historically, frequency conversion used a mechanical approach: an AC motor, fed with the input supply, drives a generator that outputs AC at the desired frequency. This arrangement made sense in an era when solid-state electronics were not robust or reliable enough for high-power applications. Rotary converters can handle large power levels and are relatively rugged but can be quite heavy, noisy, and need regular mechanical maintenance—brushes, bearings, lubrication, alignment, etc. Yet they remain relevant in certain high-power or specialized environments—like heavy industrial or older maritime—especially where robust inertia and mechanical coupling might be beneficial. -
Static or Solid-State Converters:
As power electronics advanced, robust semiconductor-based solutions emerged, leading to modern frequency conversion typically employing rectifiers, DC links, and inverters. These devices convert incoming AC to DC (through a stage using diodes or active power factor correction), then invert the DC into an AC waveform at the desired frequency (and sometimes variable voltage). They are lighter, more compact, more energy-efficient at partial loads, and require less mechanical maintenance. They also allow advanced functionality, like variable frequency drives (VFDs) that smoothly ramp from 0 Hz up to a set maximum, enabling motor speed control.
Key Functional Blocks
Regardless of technology, frequency converters involve these functional blocks:
- Input Stage: Connects to the original AC source, e.g., 220 V 50 Hz or 480 V 60 Hz.
- Rectifier or Motor: In a rotary system, an induction or synchronous motor running off the input. In a static system, a rectifier bridging the AC input into DC.
- DC Link or Intermediate Coupling: Possibly a DC bus with capacitors (solid-state) or a mechanical shaft (rotary).
- Output Generator or Inverter: For rotary, the second generator spinning at the correct speed for 50, 60, or 400 Hz. For static, an inverter (IGBTs, MOSFETs, or other power semiconductors) that synthesize the new AC waveform digitally.
- Control and Regulation: Modern converters often incorporate microcontrollers, DSPs, or advanced logic to manage waveforms, ensure stable voltage output, and protect against short circuits or load surges.
Voltage Conversion vs. Frequency Conversion
While the prime function is frequency modification, it is common for frequency converters also to handle voltage adjustments—for instance, stepping from 120 V to 230 V or vice versa. This has a trifecta effect:
- Accept the local input (e.g., 120 V, 60 Hz).
- Convert it to DC.
- Synthesize a new AC output at 230 V, 50 Hz.
Some users purely want to run a 60 Hz motor from 50 Hz supply but do not care about voltage shift if both are approximately 220–240 V. Others specifically need not just frequency changes but also a drastically different voltage level. Many frequency converters thus incorporate built-in transformers or at least an adjustable AC output stage. In short, they can address the complete mismatch—voltage and frequency—ensuring the equipment sees the power environment it was designed for.
Resonating Applications of Frequency Converters
From consumer electronics to mega industrial scenarios, frequency converters fill countless roles:
1. Running Imported or Exported Machinery
One of the most common reasons is to operate a device from one region (like the US, 60 Hz) in a 50 Hz market (EU) or vice versa. For simpler electronics, a universal power supply might do the job. But for motors, older devices, or high-power systems locked to 60 Hz, you need a converter. Factories that import specialized production lines from Japan or the US might rely on frequency converters to adapt them to the local 50 Hz environment.
2. Aerospace and Defense
Aircraft generally use 400 Hz power on board to keep motors, instrumentation, and avionics lightweight. On the ground, maintenance or testing requires 400 Hz supply for the aircraft’s systems without running engines. So ground power units (GPUs) often contain a frequency converter to supply 400 Hz from standard grid power. Naval vessels or advanced radar systems similarly might demand unique frequencies that the local port’s infrastructure does not supply natively.
3. Variable Speed Motor Control
While VFDs (Variable Frequency Drives) are not always marketed strictly as frequency converters, they do precisely that: rectify input AC to DC, then invert it at variable frequency, controlling motor speed. Many industrial lines, HVAC fans, pumps, or escalators rely on VFD technology to reduce energy consumption and mechanical stress. Here, the converter acts automatically, adjusting the motor’s frequency (and voltage) anywhere from near 0 Hz up to base or higher frequencies for speed regulation.
4. Laboratory or R&D Settings
Test labs often need to replicate the conditions of different global markets or specialized waveforms. A frequency converter with finely adjustable output frequency (and voltage) allows engineers to see how their product behaves at, say, 45 Hz or 63 Hz, or even ramp to 400 Hz for certain endurance tests. EMC (electromagnetic compatibility) labs might also use these capabilities to measure equipment performance or compliance.
5. Generator and Microgrid Integration
In some microgrid or generator setups, a device might produce AC at variable frequency linked to the prime mover speed. A converter can condition that, yielding a stable 50 or 60 Hz feed to the local load or tie it to a mainstream grid. Progressive distributed energy resources also harness advanced inverters that effectively do frequency conversion to feed the local microgrid or the public network with stable waveforms.
6. Maritime and Offshore
Ships with specific on-board frequencies can connect to shore power (cold ironing) in port, but often the shore is at a different frequency than the ship’s system. The solution is a frequency converter that ties them seamlessly. This reduces emissions and engine usage in port, a big impetus for “green port” initiatives. Offshore platforms might face the same scenario with support vessels, each built to different standards.
Rotary vs. Solid-State Frequency Converters in Detail
Although the broad categories have been introduced, expanding the specifics clarifies why certain industries still embrace one approach or the other.
Rotary Converters
- Principle: A large motor, typically a three-phase induction or synchronous motor, drives an AC generator with the desired output frequency.
- Pros:
- High overload capacity: The mechanical inertia can buffer short bursts of load change.
- Simplicity in older or robust environments, minimal power electronics concerns.
- Tolerance to certain distortions: The mechanical system might not be as sensitive to input waveform anomalies.
- Cons:
- Heavier, physically larger, more noise and vibration.
- Requires mechanical upkeep: bearings, lubrication, possibly brush gear for certain designs.
- Lower efficiency than well-designed static solutions.
Static (Solid-State) Converters
- Principle: Power electronics, typically with IGBT or MOSFET-based inverters, rectify input AC to a DC link, then re-invert at the new frequency.
- Pros:
- Compact, efficient, no moving mechanical parts.
- Advanced features: variable frequency, soft start, remote control, digital monitoring.
- Minimal maintenance.
- Cons:
- Sensitive to input power quality, harmonic distortions, or transients, requiring protective circuits.
- Possibly produce harmonic emissions themselves, needing filters.
- Complex electronics can be susceptible to extreme temperature or environment if not built for it.
In modern contexts, large power and broad usage typically lean toward advanced solid-state designs. Rotary units survive in niche or legacy heavy-power conditions, or in places where robust mechanical inertia benefits the system.
Sizing and Selecting a Frequency Converter
Choosing the right converter is critical to ensure reliability, cost-effectiveness, and performance. Key considerations:
-
Power Rating (kVA or kW)
- The converter capacity must exceed or at least match the load’s maximum demand. For motor loads, consider inrush current or starting torque. A margin is typically recommended—like 20–25% above the maximum expected load.
- Evaluate power factor and starting surges, especially for big inductive loads.
-
Input and Output Voltage
- Confirm if you need step-up, step-down, or a pass-through scenario. If your machine only requires frequency shift at the same approximate voltage (like 220 V to 220 V, or 3-phase 400 V to 400 V), you can pick a simpler design. If you specifically want 110 V, 60 Hz from 230 V, 50 Hz, ensure the converter includes an appropriate transformer or has a variable output stage.
-
Phase Requirements
- Many industrial or heavy applications need three-phase output. If your supply is single-phase but you want a three-phase output, the converter must be designed for that. In consumer-level usage, you might only handle single-phase in and out.
-
Frequency Range
- A typical converter might output a fixed 50 or 60 Hz. If you require variable from, say, 10 Hz up to 400 Hz, that is a more specialized or advanced system akin to variable frequency drives or lab power supplies.
-
Environment and Duty Cycle
- Will it operate continuously in a hot environment, or only occasionally? Is the location a clean lab or a dusty factory floor? Look for designs rated for the correct temperature, humidity, IP enclosure rating, or relevant MIL-STD if in defense.
-
Harmonic Distortions
- Solid-state converters can generate harmonics. If you are in a sensitive environment, choose a design with active front ends or filters to keep the total harmonic distortion (THD) low.
-
Control Features
- Modern converters may offer user-friendly LCDs, remote control via Ethernet or RS-485, alarm logs, advanced fault diagnostics, or synchronization capabilities to parallel with other sources.
-
Budget and Life-cycle Costs
- The purchase cost of a converter is not the only factor. Maintenance, efficiency, reliability, and potential downtime matter. In some high-need industries, a cheaper or simpler device that fails more often becomes more expensive in the long run.
-
Compliance
- Certain industries (aerospace, military, maritime) require compliance with standards like MIL-STD-810, MIL-STD-901, or marine classification society rules. Ensure the converter is tested or certified if necessary.
Efficiency and Power Quality
Frequency converters inherently process power, so some energy losses occur. The efficiency depends on design, load level, and technology:
- Rotary Efficiency: Might vary widely, from 80% to 95%, typically lower for older or smaller sets. Losses include mechanical friction, windage, and electrical conduction in the motors/generators.
- Solid-State Efficiency: Often in the 90–98% range, depending on design and load. Typically better than rotating solutions, but still a few percent are lost in semiconductor switching and conduction.
Because converters can also produce or mitigate harmonic content, some advanced solutions incorporate power factor correction or harmonic filters at the input or output stage, improving the overall power quality. High-quality devices keep input current near sinusoidal and output waveforms with minimal distortion. Some also handle unbalanced loads gracefully, especially in multi-phase setups.
Implementation Scenarios
1. Industrial Production Lines
Consider a global company that purchases specialized manufacturing machines from a US vendor (60 Hz) for deployment in Europe (50 Hz). A large frequency converter is installed—likely a solid-state system with capacity of tens or hundreds of kVA. The line integrates power factor correction, real-time load balancing, and ensures stable 60 Hz to the machines. Meanwhile, in the rest of the facility, local 50 Hz remains unaffected. The converter’s digital interface logs energy usage, alarms for fault conditions, and ensures minimal reliance on mechanical adjustments.
2. Aircraft Ground Support
At an airport, 400 Hz ground power units feed planes parked at gates. These might be separate standalone carts or integrated in the jet bridge. The underlying frequency converter might accept local 50 or 60 Hz utility power, rectify it, then produce the 115 V AC, 400 Hz that most aircraft systems need. The GPU is sized to handle typical plane loads—operating lights, climate control, avionics—for comfortable preflight checks. Efficiency and reliability are paramount, as delayed flights cost millions. The design might also incorporate advanced electronics to handle large inrush from various systems on the plane.
3. Motor Speed Control in HVAC
In large buildings, fans or pumps for air conditioning or water circulation often implement VFDs to slow or speed them up based on demand. Although the overarching concept is controlling speed, the device is effectively a frequency converter with an integrally variable output. The building automation system can ramp speeds down for energy savings or ramp up as needed. Each dimension—peak torque, ramp time, harmonic compliance—finds solutions in a well-chosen drive. The occupant experiences comfortable airflow or stable water pressure with minimal wasted electricity.
4. Laboratory Testing
A product manufacturer runs a global compliance test lab. They might replicate the power environment of any major grid on Earth: 230 V, 50 Hz (European), 120 V, 60 Hz (US), 100 V, 50/60 Hz (Japan), or even custom waveforms. Using a programmable frequency converter, the lab staff can set voltage, frequency, ramp profiles, and measure how the device under test reacts. This is crucial for product safety testing, performance checks, or stress tests. The converter’s user interface might allow specifying 47–63 Hz or even up to 400 Hz, simulating supply anomalies. Possibly, advanced software logs wave distortion or measures device leakage current.
Maintenance and Care
Whether mechanical or electronic, a frequency converter does require suitable environment and periodic checks:
- Rotary: Inspect mechanical couplings, bearings, alignment, belts if any, lubrication intervals. Observe brush gear if it’s a synchronous design. Regularly check for vibration or unusual noise.
- Solid-State: Keep the heat sinks or fans clean. Monitor for dust accumulation that can hamper cooling. Possibly check fan or filter replacements on recommended cycles. Inspect DC bus capacitors for aging. Also ensure firmware updates if the device is microprocessor-based.
- Cooling: Heavier load means more heat generation. Good ventilation or forced-air cooling is standard. Large units might use liquid cooling in extreme scenarios. Ensure all thermal trips or sensors operate properly.
- Calibration and Settings: If you have adjustable output frequency or voltage, confirm the setpoints occasionally. A mismatch could hamper motor operation or hamper your test results.
- Firmware or Software: Some advanced units incorporate local logs or network connectivity. Maintaining the software or protocols ensures you can spot trends or preempt failures.
Economic Perspective
At first glance, one might question if the cost of procuring a frequency converter outweighs simpler alternatives—like universal power supplies or redesigning the motor. In many industrial or specialized contexts, it is not only about cost but also about feasibility:
- Large Motors: Rewinding or re-engineering a motor for 50 vs. 60 Hz is expensive, plus might degrade performance. A converter is more straightforward.
- Machinery that Must Retain Original Specs: Complex production lines or specialized devices might revolve around a particular speed or an integral relationship to 60 Hz.
- Operational Efficiency: VFD-based converters can yield energy savings by letting motors operate at partial speed. This can offset the converter’s capital cost via lower electricity bills or extended mechanical life.
- Integration: If you do short-run tests or produce multiple versions of a product for different markets, a single converter-based approach can unify your test stands, saving duplication.
Additionally, for some high-power cases, a single central converter might feed multiple machines, distributing the cost across them, and providing a stable frequency environment for the entire operation. Over the device’s lifetime, the reliability gained, and maintenance or logistic simplifications can produce intangible yet significant ROI.
The Future Trajectory of Frequency Converters
Power electronics is a fast-evolving domain. Ongoing trends predict:
- Higher Efficiency Semiconductors
Introduction of wide bandgap materials (SiC - Silicon Carbide, GaN - Gallium Nitride) can reduce switching losses, boost power density, and shrink heat generation. Frequency converters will become more compact, with improved energy efficiency, lowering operational costs. - Smarter Control
Embedded controllers and connectivity pave the way for real-time data logging, predictive maintenance, fault diagnosis, and remote field updates. Converters might auto-adjust parameters based on load patterns, grid conditions, or advanced AI algorithms. - Greater Power Density
For aerospace or defense usage, ever-lighter solutions matter. We might see new topologies—multi-level inverters, resonant circuits—that push converter performance to new heights while meeting strict reliability standards. - Renewable Microgrids
As microgrids and distributed generation flourish, frequency converters bridging DC sources (PV, batteries) or dealing with variable frequency generation from wind turbines become standard. They may evolve into multi-functional “power hubs” controlling real and reactive power, voltage, and advanced fault-tolerant modes. - Integration with Energy Storage
A converter might coordinate the exchange of power between battery banks and the AC bus, modulating frequency if operating as an islanded microgrid. Frequency, real, and reactive power flows could be orchestrated to keep the microgrid stable.
In short, frequency converters, once specialized devices for bridging 50–60 Hz or generating 400 Hz for aircraft, are morphing into sophisticated enablers for the new energy landscape, underpinned by modern electronics, advanced control, and integrated data intelligence.
Best Practices for Frequency Converter Usage
To maximize your converter’s lifespan and performance:
- Correct Sizing: Overrating is safer than borderline capacity. Cater for motor inrush or short-term surge loads.
- Clean Environment: Ensure minimal dust, moisture, or extreme temperature. Consider enclosures or IP ratings if needed.
- Stable Supply: An upstream voltage stabilizer or surge protector helps avoid input disruptions harming the converter.
- Monitoring: Periodically check the internal logs or external instrumentation for unusual waveforms, temperature warnings, or load anomalies.
- Competent Installation: Qualified electricians or engineers should handle wiring, especially for three-phase or high-voltage setups. Observing polarity, grounding, and torque specs is essential.
- Vendor Support: If your usage is mission-critical, pick a brand with robust spares availability, firmware updates, local support, and proven references in your industry.
Troubleshooting Common Issues
- No Output: Could be an input fuse or breaker tripped, or the converter’s internal power supply. Check the control panel for error codes.
- Overheating: Possibly excessive load beyond rating, clogged air filters, or failing fans. Inspect the environment and load profile.
- Harmonic Distortion: If the converter or load connected is producing undesirable harmonics on the supply, consider adding filters or adjusting the converter’s settings.
- Voltage Drop: The converter might not be configured for correct output voltage, or input voltage is sagging under heavy load. Measure line voltages carefully.
- Over Current Fault: The load may exceed the converter’s design, or a motor starting current is too high—some converters have built-in motor start modes or soft start features to handle that gracefully.
- Mechanical Noise (Rotary): Worn bearings or alignment drift in older motor-generators can produce vibrations. Address promptly to avoid catastrophic failure.
Conclusion
The Frequency Converter is far more than a niche solution. It stands as a linchpin that empowers countless cross-border industrial applications, from running machinery globally to controlling motor speeds in advanced factory lines, from reliably delivering 400 Hz to an aircraft’s electrical system to ensuring precise lab power conditions. By bridging differences in frequency and often voltage, it has become integral to modern global commerce, standardizing test procedures, enabling large-scale equipment mobility, and supporting the next generation of microgrids and energy systems.
Though the principle can be straightforward—transform one AC frequency to another—under the hood, a frequency converter may come in either a robust rotary format or a cutting-edge solid-state design loaded with IGBT-based inverters and smart microcontrollers. Each approach has pros and cons. Rotary units excel in certain high-inertia or legacy setups, while static converters typically offer lighter weight, higher efficiency, better adaptability, and less mechanical upkeep.
Implementation across industries reveals that these devices keep supply conditions stable, help motors remain within their intended operating speeds, and ensure sensitive electronics get the correct waveforms. On the higher-level scale, frequency converters become the cornerstones of dynamic grid management, bridging microgrids with main networks or enabling 400 Hz aviation power. In the contemporary push towards green, smart, and flexible power systems, their role only looks set to expand as better semiconductors, advanced controls, and integrated intelligence push performance boundaries.
If you are in the market for a frequency converter—be that for a personal workshop to run imported tools, a specialized test lab with multi-frequency demands, or a large industrial operation—understanding the fundamentals clarifies your purchasing, integrating, and maintenance strategies. Evaluate your load’s power rating, consider the environment, plan for possible voltage shifts, and weigh the cost of super advanced features against your real needs. Periodic care, verifying correct input supply, and respecting load surges ensure the device enjoys a long service life. And as more systems adopt or rely on frequency conversion for advanced energy management, we can expect a future where the boundaries of 50 Hz or 60 Hz gradually matter less, overshadowed by the ability to generate exactly the waveform you need for your device or grid.