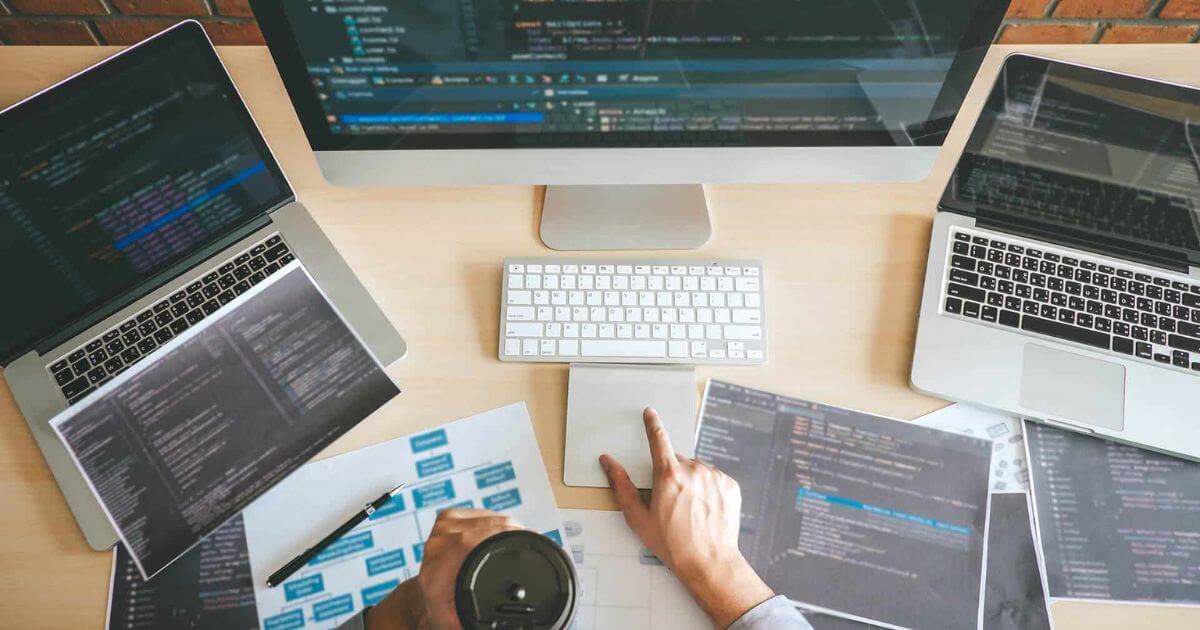
Torque Converter
Convert torque units quickly and accurately.
Introduction
In the world of automotive engineering, few components are as crucial—yet often overlooked by everyday drivers—as the torque converter. Found primarily in vehicles with automatic transmissions, it quietly carries out the essential job of transferring rotational power from the engine to the transmission. Unlike a manual car, which uses a mechanical clutch, automatic vehicles rely on a fluid connection that needs to slip enough to allow the engine to keep running at idle and engage strongly enough to propel the vehicle when accelerating. That fluid-based coupling is the torque converter. In essence, this unique device eliminates the need for a clutch pedal while ensuring smooth power delivery.
Driven by principles of fluid dynamics, a torque converter might look unassuming—a circular metal housing with a few internal components—but it performs a pivotal function. When your engine is running, the torque converter is constantly working behind the scenes, modulating power so you can shift gears seamlessly and enjoy a refined driving experience. But how does it do all this? Why do we not notice it in everyday use? And why is it so important to match the right torque converter to performance goals in drag racing or towing applications?
In this comprehensive article, we take a deep dive into what a torque converter is, how it operates, different design features, and the benefits (and sometimes pitfalls) that come from selecting or servicing these devices. We will also look at ways the torque converter has evolved to meet modern demands—from standard everyday vehicles that prize fuel economy, to performance racing torque converters optimized for track success. By the end, you will have a thorough grasp of the science, mechanics, and applications behind the torque converter, shedding light on an often underestimated but widely used piece of automotive hardware.
What is a Torque Converter?
A torque converter is, at its core, a type of fluid coupling. Fluid couplings are devices that rely on the flow of fluid—transmission fluid, in automotive contexts—to transfer rotational power from one shaft to another, without requiring a direct mechanical linkage like a clutch. While a standard fluid coupling simply matches rotational speed between input and output, a torque converter is more sophisticated, incorporating extra features that allow for torque multiplication at lower speeds, and a lockup mechanism to improve efficiency at cruising speeds.
Physically, a torque converter is typically found between the engine (the prime mover) and the automatic transmission (the driven load). When you start your vehicle and the engine is running, the converter is spinning, allowing the engine to keep turning even if the transmission is in drive gear and the wheels are stationary. Unlike a manual transmission, where pressing the clutch disconnects the engine from the gearbox, the torque converter is always coupled to the engine but manages slip fluidly.
For a typical passenger car, a torque converter allows the driver to simply move the gear selector to Drive and press the accelerator, without worrying about stalling or coordinating pedal and gear shifts. The converter manages torque flow seamlessly from idle all the way to highway speeds.
Main Components of a Torque Converter
-
Pump (Impeller)
This part is attached to the engine’s crankshaft, so it spins at the same speed as the engine. Shaped like a fan or impeller, the pump propels transmission fluid outward by centrifugal force. High-velocity fluid is ejected from the pump’s blades and directed toward the torque converter’s next major component. -
Turbine
The turbine faces the pump inside the torque converter shell. When the high-speed fluid from the pump hits the turbine blades, it causes the turbine to spin. This turbine is connected to the transmission’s input shaft. As a result, the rotational movement fluid carries is transferred to the turbine, which in turn spins the gearbox. -
Stator (or Reactor)
Wedged between the pump and the turbine is the stator. The stator sits on a one-way clutch mechanism and plays a pivotal role in torque multiplication at lower speeds. When fluid flows from the turbine back to the pump, the stator re-directs it so that it helps push the turbine again, effectively boosting torque. Under higher speeds, once fluid flow patterns change, the stator “freewheels,” reducing its effect. -
Lockup Clutch
Many modern torque converters include a lockup clutch (or lockup mechanism). When the vehicle hits cruising speed, this clutch can engage to lock the turbine and pump together, essentially removing the slip that typically occurs in fluid couplings. By doing this, the lockup clutch boosts fuel efficiency and lowers transmission fluid heating, because the input and output rotate at a 1:1 ratio. -
Housing
The entire assembly—pump, turbine, stator—sits within a welded metal housing shaped like a doughnut. The outer shell attaches to the flywheel or flexplate of the engine, ensuring the torque converter rotates with the crankshaft. It also contains the transmission fluid that circulates within.
How the Torque Converter Works
To understand the torque converter’s operation, consider what happens when you press the accelerator from a standstill:
-
Idle and Starting
The engine is spinning, so the pump portion of the torque converter also spins. Fluid is flung outward and hits the turbine, which starts to rotate. At very low speeds, there is an internal fluid swirl that leads to torque multiplication thanks to the stator’s guidance of fluid. This let’s the vehicle pull away from a stop without stalling the engine or needing a manual clutch. -
Acceleration
As you press the accelerator, more torque is provided by the engine, the pump spins faster, fluid moves with increased velocity, and the turbine speeds up. Meanwhile, the stator re-directs returning fluid to reinforce the pump’s fluid flow at the turbine. This yields a torque multiplication effect, typically in the range of 1.5 to 2.5 times the engine torque (depending on design). This advantage is especially notable for heavier vehicles, or during towing, or for high-performance situations. -
Cruising and Lockup
Once at higher speeds—cruising on a highway, for instance—less torque multiplication is required. The difference in rotational speed between the engine (pump) and the transmission input (turbine) becomes smaller. Fluid flow changes, the stator can freewheel, reducing internal drag. Meanwhile, the lockup clutch engages in modern torque converters, coupling the turbine and pump together, so there is nearly zero slip. This improves efficiency, since fluid friction no longer saps energy. -
Deceleration or Stopping
When the vehicle slows down or stops with the brakes engaged, the turbine slows, but the engine can keep turning. The fluid coupling aspect allows slip, so the engine does not stall. That is primarily why you do not need to manually disengage a clutch in an automatic vehicle.
Why Use a Torque Converter Instead of a Clutch?
Automatic Transmissions: A conventional mechanical clutch connects and disconnects the engine from the gearbox by friction. However, an automatic car is designed to shift gears smoothly without direct driver input. The torque converter’s fluid-based coupling is more forgiving, letting the engine idle with minimal load, and allowing for “creep” motion at low speeds. Also, by providing torque multiplication at low RPM, the torque converter aids in smoother, more potent starts from rest.
Ease of Operation: The torque converter’s main advantage for everyday drivers is that the process is seamless—no manual pedal, no risk of stalling from poor clutch control. For many, that convenience is enough. In specialized contexts, though, some prefer manual transmissions for direct mechanical engagement or track performance. But advanced torque converter designs have bridged some of that performance gap.
Torque Multiplication: Key to Launch Performance
One unique characteristic of a torque converter is its ability to multiply engine torque at lower speeds, something a simple fluid coupling cannot do. When the pump’s velocity is high, but the turbine is relatively slow (like when accelerating from a stop), fluid hits the stator and is re-directed advantageously, amplifying torque. This effect typically diminishes once the turbine catches up to the pump speed. You get an initial boost, often referred to as the “stall torque ratio,” which can be valuable in heavy vehicles, towing, or performance racing where a strong launch is essential.
Lockup Mechanisms and Efficiency Gains
Classic torque converters from decades ago had an inherent efficiency penalty on highways, as there was always some slip in the fluid coupling. This slip meant extra fuel consumption and heat generation. To mitigate that, automotive engineers introduced the lockup clutch: a friction disc or mechanical link inside the converter that can clamp the turbine and pump together.
When you are cruising at a steady speed in top gear, the engine’s electronic controls or the transmission computer triggers the lockup. Fluid slip disappears, rotational speeds match, and the converter acts like a direct mechanical coupling. This yields better fuel economy, less fluid heating, and a more direct throttle response.
Torque Converter Stall Speed
The “stall speed” is the engine RPM at which the converter “stalls” the engine if the output shaft is not allowed to rotate. In simpler terms, imagine your automatic-transmission vehicle’s wheels are locked in place (like pressing the brakes firmly or jacking up the drive axle so it cannot turn). You step on the accelerator. The engine speed will rise to a certain point—the stall speed—and the torque converter can’t let it rev higher because fluid coupling saturates. That stall speed is related to converter design, and it heavily influences how the vehicle feels when you start from rest.
- Lower Stall Speed: The converter might “hook up” earlier, beneficial for fuel economy and normal driving.
- Higher Stall Speed: More slip is allowed before the converter transmits full torque. This can lead to stronger acceleration off the line for performance driving or drag racing.
Performers in drag racing or off-road often pick specialized high-stall torque converters that let the engine rev into its power band before launching.
Upgrading and Customizing Torque Converters in Performance Applications
High-performance enthusiasts, drag racers, or those towing heavy loads might replace their stock torque converter with an aftermarket alternative. Why?
-
Stall Speed Optimization: A well-chosen converter ensures the engine can rev at a more powerful range before friction fully engages, yielding better 60-foot times at the drag strip or more robust towing capability.
-
Stronger Internal Components: Performance converters often feature improved impeller designs, furnace-brazed fins, or ballooning-resistant housings to cope with higher torque.
-
Finer Tuning: Some converters are built or restalled specifically for an engine’s torque curve, gear ratios, and intended usage. This custom approach yields maximum synergy.
-
Lockup vs. Non-Lockup: Detailed calibrations might be done to refine lockup clutch engagement for minimal slip at higher speeds.
Common Myths and Misconceptions
-
Torque Converters Always Waste Fuel: Older designs indeed produced more slip and lower efficiency at highway speeds. Modern designs with lockup clutches drastically reduce that slip once at cruising speeds.
-
They Are Only for Convenience: In performance drag racing or specialized vehicles, a torque converter can yield a big advantage in off-the-line acceleration due to torque multiplication.
-
All Horsepower is Lost: While there is some fluid friction, an optimized converter transfers power quite effectively. Gains at launch can offset minor slip at mid-range speeds.
-
You Never Need to Service a Torque Converter: While typically sealed, torque converters still rely on transmission fluid shared with the gearbox. Proper fluid changes are critical for longevity, as well as ensuring the lockup mechanism remains functional. In some cases, a converter might develop problems, requiring refurbishment or replacement.
Common Issues and Symptoms of Converter Failure
- Slipping at Higher Speeds: If the engine revs up but the vehicle does not accelerate proportionally, the converter lockup might be malfunctioning or the internal fins are damaged.
- Overheating Transmission Fluid: Excessive slip or a malfunctioning stator can cause more heat build-up.
- Shudder at Cruising Speeds: If the lockup clutch engages but chatters, you might feel a vibration or shudder.
- Delayed or Harsh Engagement: If you shift to Drive and it takes a while for the car to move, it can indicate internal fluid coupling issues or a failing stator one-way clutch.
- Abnormal Sounds: Banging, rattling, or whining from the converter area could be damaged blades or bearings.
Diagnosis typically involves torque converter tests, scanning for TCC (Torque Converter Clutch) lockup codes, checking fluid conditions, and sometimes dropping the transmission pan to investigate further.
Variations and Specialized Designs
-
Three-Element vs. Four-Element: The standard automotive torque converter is typically three-element (pump, turbine, stator). There are also older or specialized fluid couplings or certain heavy-duty variations.
-
Multiple-Disc Lockup: Some high-end or heavy-duty torque converters use multiple friction discs for the lockup to handle more torque or repeated rigorous engagement.
-
Industrial Torque Converters: Heavy machinery or marine applications might have larger, robust fluid couplings or torque converters to manage massive loads.
-
Electronic Controls: Modern transmissions integrate solenoids or electronics to modulate lockup precisely, merging it with gear shifts for maximum efficiency, minimal shift shock, or emissions compliance.
Installing or Replacing a Torque Converter
Replacing or upgrading typically demands removing the transmission from the vehicle, a major job. Key steps:
-
Transmission Removal: The converter is bolted to the flexplate on the engine side, and also seats onto the transmission input shaft. One must unbolt the converter from the flexplate, unfasten the bellhousing, and carefully remove the entire transmission.
-
Inspecting the Old Converter: Checking the fluid inside for metal debris or discoloration might highlight problems in the gearbox.
-
Mounting the New Converter: Careful alignment is crucial. The new or rebuilt converter must seat fully onto the transmission input shaft, ensuring the pump drive tangs engage.
-
Check for Proper Clearance: Typically, you measure or confirm minimal but adequate clearance between the flexplate and converter pads to avoid thrust issues.
-
Refilling with Proper Fluid: Different transmissions require different fluid specs. Using the correct fluid matters for converter function and longevity.
Industry Applications Outside Passenger Cars
While best known for passenger vehicles with automatic gearboxes, torque converters appear in many other settings:
-
Off-Highway / Construction: Bulldozers, heavy loaders, and agricultural equipment often use robust converters, ensuring no stalling under load, plus torque multiplication is helpful for heavy pulling or pushing.
-
Industrial Power Units: Some stationary engines rely on fluid couplings or torque converters to drive large pumps, fans, or conveyors.
-
Marine Transmissions: Certain boat or ship propulsion systems incorporate torque converters for smooth power transitions.
-
Racing: Drag racers, circle track cars, and other motorsport classes have custom or high-stall torque converters to optimize launch.
Looking Ahead: Innovations in Torque Converter Technology
While the basic torque converter remains conceptually similar to older designs, modern engineering has introduced:
- Improved Lockup Control: Automatic transmissions stage the lockup at lower speeds or partial throttle, improving efficiency.
- Electronically Manageable Stall Characteristics: Some advanced transmissions can vary fluid pressure or stator fin angles.
- Materials: Use of better steels, brazing techniques, or carbon-based friction materials for lockup clutches to handle high torque and resist wear.
In parallel, new wave transmissions—like dual-clutch or continuously variable transmissions (CVTs)—sidestep a torque converter altogether, using alternate friction mechanisms or belt/pulley systems. Still, torque converters remain a standard in many automatic transmissions because of their proven smoothness, reliability, and torque multiplication.
Selecting the Right Torque Converter for a Custom Build
If you are building or modifying a vehicle:
-
Match Stall Speed to Engine Torque Band: A performance engine with a high RPM torque peak might flourish with a higher stall converter. A mild street engine might do best with a near stock or slightly higher stall.
-
Consider Rear Axle Ratio and Vehicle Weight: Heavier cars or deeper gear ratios can handle a bit more stall, as it helps get off the line. Light cars might not need as high.
-
Transmission Type: Some transmissions have mechanical differences that interact with the torque converter design. For instance, GM’s 4L60E converters differ from 4L80E or 6L80 transmissions in mounting or lockup strategy.
-
Intended Use: Street driving wants a converter that locks up quickly for fuel economy, while drag racing might want maximum stall for initial acceleration. Towing rigs or off-road might want torque multiplication for low-end grunt.
-
Reputable Builders: Many performance shops specialize in torque converter rebuilds, balancing, and customization. They might question your engine’s horsepower, torque curve, gear ratio, tire size, and usage to propose an optimal converter.
Signs You May Need a Torque Converter Upgrade or Replacement
- High-Performance Engine: If you installed a big camshaft, raising your engine’s power band, a stock converter might hamper performance off-idle.
- Transmission Overheating: Excess slip from a failing or mismatched converter can cause heat buildup in automatic transmissions. Once you confirm other cooling steps are fine, it might be time for a converter fix.
- Shuddering on Lockup: Sign of friction material or fluid breakdown.
- Strange Noises or Slipping: A damaged stator sprag or bent turbine blades can degrade performance severely.
Basic Maintenance
Generally, the torque converter is sealed and does not require direct “maintenance” individually. Instead, you maintain it by:
- Regular Transmission Fluid Changes: Old, burnt fluid undermines torque converter operation.
- Adequate Cooling: Heat is the enemy. Ensuring the transmission cooler is functioning well keeps fluid temperature in check.
- Respecting Towing Limits: Overloading or hauling significantly beyond rating can overwork the converter, generating excessive heat.
Conclusion
Though overshadowed by the more obvious features of an automobile, the torque converter is a marvel of fluid dynamics and mechanical design. It seamlessly handles engagement from idle to high speed, multiplies torque during acceleration, spares drivers from using a hand or foot-operated clutch, and enhances overall comfort for everyday commuting. Whether you drive a standard family sedan, a high-performance drag car, or a heavy construction vehicle, chances are a torque converter (or a variant) is playing a fundamental role in transferring power from your engine to the wheels.
Beyond daily commuting, torque converters come in specialized flavors for racing, towing, and industrial use. Their design intricacies—like stall speed, lockup clutch, fin angle, and stator function—can be tailored to the exact nature of a powertrain. Over the past decades, engineers have refined these fluid couplings to boost fuel economy (via lockup mechanisms), sharpen performance (via custom stall speeds), and maintain robust durability (via advanced brazing and materials).
For a driver or hobbyist, understanding how a torque converter operates can transform how you see an automatic transmission. If you like high-performance modifications or plan to push your vehicle harder, an appropriate torque converter might be one of the single most impactful upgrades—dramatically changing launch feel and acceleration. Likewise, if an older automatic car starts to show signs of slippage or poor efficiency, investigating the torque converter’s health is a prudent step.
In the end, the torque converter is more than a bridging device; it exemplifies the synergy between fluid mechanics and mechanical engineering. Its quiet reliability underpins countless smooth starts and comfortable rides, while specialized variations hail from racetrack to farmland. By gaining insight into its operation, design, and potential pitfalls, you stand better equipped to appreciate why automatic transmissions have revolutionized driving ease—and how that revolution continues to refine and adapt through each new generation of torque converters.